Digital Lean Manufacturing Quantifying the Financial Impact of Industry 40 Integration in 2024
Digital Lean Manufacturing Quantifying the Financial Impact of Industry 40 Integration in 2024 - Projected cost reductions through digital lean manufacturing in 2024
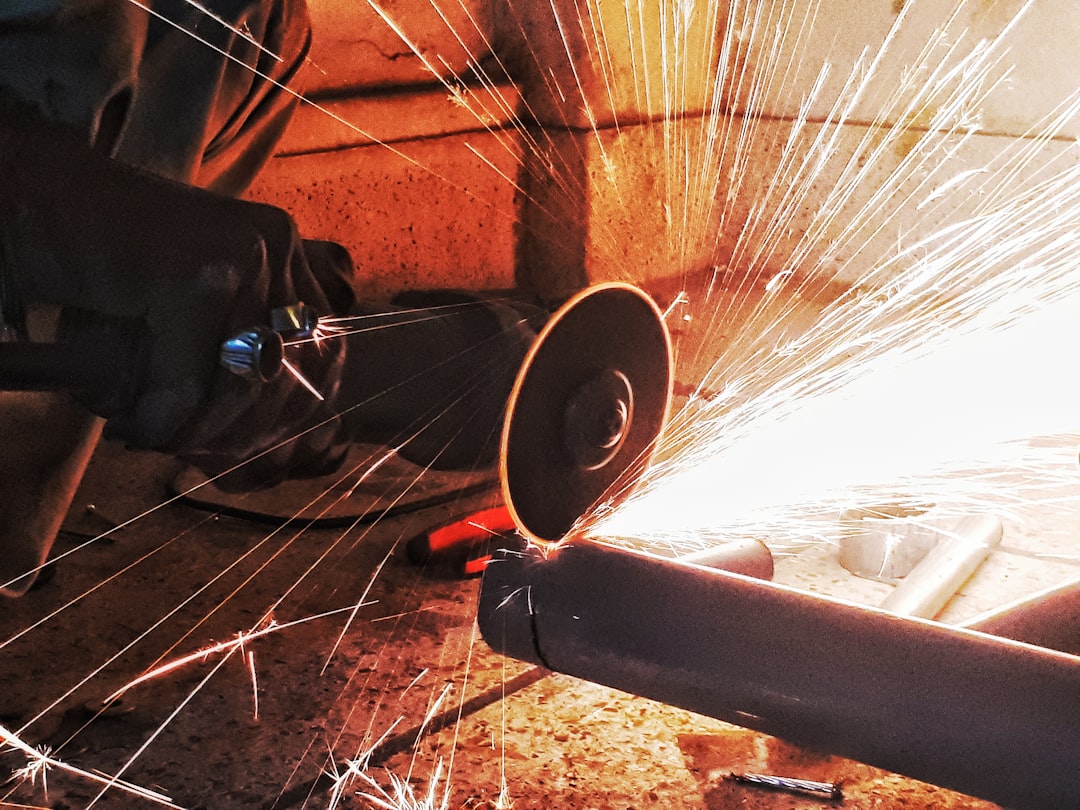
The potential for cost reductions through digital lean manufacturing in 2024 is significant. While traditional methods have brought about efficiency improvements, incorporating Industry 4.0 technologies promises to amplify those gains. This fusion of digital tools and established processes can refine operations, reduce waste, and boost overall efficiency.
However, the path to unlocking this potential isn't without its challenges. Many manufacturers are struggling to move beyond initial trials and fully integrate these technologies. Cybersecurity concerns are also rising, highlighting the importance of securing data and systems. Amidst a volatile market and heightened focus on cost control, companies must navigate these hurdles to capitalize on the benefits of digital lean manufacturing.
The idea of "digital lean manufacturing" is intriguing. It sounds like the next big thing in manufacturing, promising significant cost savings. We're talking about a 30% reduction in operating costs by 2024, which is nothing to sneeze at. The projected savings are attributed to various factors, including the adoption of machine learning, the internet of things, digital twins, and augmented reality.
One interesting development is the use of machine learning for predictive maintenance, which could reduce unplanned downtime by 20%. This could potentially lead to significant savings in maintenance costs. The integration of IoT devices is expected to streamline supply chain management, reducing excess inventory costs by an estimated 15%.
I'm curious about the impact of digital twin technology. If these models can reduce prototype development costs by 25%, it would be a game-changer for many companies. While the idea of AR training programs improving workforce productivity by 20% is promising, I wonder about the practicality of implementing such programs across diverse manufacturing environments.
Another potential benefit is a 18% reduction in energy consumption. That's a huge saving, and it's commendable that the focus is shifting towards sustainability. However, I'm cautious about the predicted payback period of less than two years for the investments in digital lean manufacturing. While the projections are encouraging, it's important to consider the complexity and the potential challenges in implementing these technologies on a large scale.
Digital Lean Manufacturing Quantifying the Financial Impact of Industry 40 Integration in 2024 - Challenges in aligning lean principles with Industry 0 technologies

The idea of merging lean principles with Industry 4.0 technologies, often dubbed "Industry 0," sounds great on paper. It's supposed to lead to huge profits by making factories run smoother and more efficiently. The hope is that companies can use advanced digital tools to achieve even greater waste reduction, leading to lower costs and better profits.
In theory, "Industry 0" lets companies see everything happening in their factories in real-time and automate processes, allowing for quicker adjustments to changing market demands. This is great, but the reality is that many companies are still stuck in the testing phase and haven't made these new tools a permanent part of their operations.
It's clear that the companies who successfully merge these two approaches will be way ahead of their competition. But there are some big challenges to overcome. For one thing, some people believe that Industry 4.0 technologies will completely replace lean principles, which isn't true. They should be seen as partners, with each making the other better.
Another big hurdle is figuring out how to manage the technological changes while also thinking about the human side of things. It takes careful planning to make sure workers are ready and willing to use these new technologies.
The big question is how to get past the initial testing phase and make these technologies a standard part of how companies do business. If companies can't make that jump, they'll never see the big financial gains they're hoping for.
Companies need to look closely at both the technology and their organization's readiness to adopt this approach. If they do that, then "Industry 0" has the potential to be a game changer for manufacturing.
There's a lot of buzz about combining lean manufacturing principles with Industry 4.0 technologies – they call it "Industry 0." The idea is that these two approaches will work together to make companies more efficient and profitable. But it's not all sunshine and rainbows. There are some real challenges that companies need to overcome if they want to make this work.
One issue is that Industry 4.0 is all about rapid innovation, while lean manufacturing is all about eliminating waste. These two ideas don't always sit well together. It's like trying to put a square peg in a round hole. A company might be hesitant to adopt new technologies if it's worried about disrupting its established processes, even if those processes are inefficient. This tension between innovation and efficiency can lead to delays in implementing new technologies.
Then there's the fact that a lot of lean initiatives fail to meet their goals. Research shows that 70% of these efforts fall short. Why? Because companies often don't integrate these new technologies properly into their systems. They also fail to give their employees enough training to adapt to new processes.
It seems that traditional lean methods, which are designed for gradual improvements, sometimes clash with the more disruptive nature of Industry 4.0. This can lead to slow decision-making, and in today's fast-paced world, companies need to be quick on their feet.
Industry 4.0 relies heavily on data analytics, but this can cause problems in lean environments. Lean is all about standard processes, which don't always leave room for flexibility. So, even if companies have access to real-time data insights, it might be difficult to make changes to their established processes.
It's also important to remember that Industry 4.0 involves a lot of interconnected devices and systems, which means there's an increased risk of security breaches. This is a huge issue when it comes to lean principles, because lean is all about minimizing waste. A cyberattack could easily disrupt a lean operation, potentially negating all those hard-won efficiency gains.
Lean is based on the idea of engaging employees and constantly improving. However, implementing automated technologies can lead to resistance from workers who might feel like their jobs are being threatened. This is a real hurdle that needs to be addressed, or companies risk facing a lot of pushback from their employees.
Research shows that a lack of alignment between management goals and practical execution is a huge barrier to implementing lean transformations. This suggests that companies need to have clear strategies and make sure that everyone is on board with the plan to adopt digital tools.
The Internet of Things (IoT) can add to the complexity of lean implementations. Companies can end up with so much data that it's overwhelming and difficult to make sense of it all. Rather than helping make decisions, the data can actually hinder decision-making, which is the opposite of what companies want to achieve.
Even with promising new technologies like predictive maintenance, there are challenges. Predictive maintenance relies heavily on collecting and analyzing data, and this can be a bottleneck if companies are still using outdated systems.
It's easy to be seduced by the idea of a short payback period for Industry 4.0 investments. But companies need to be realistic. These transitions are complicated, and they often take longer and cost more than initially anticipated. Many companies end up facing technical and managerial hurdles that delay their return on investment.
Ultimately, the success of "Industry 0" hinges on its ability to allocate resources better, drive efficiency, and increase profit margins. The potential is there, but it's important to acknowledge and overcome the challenges before jumping in headfirst.
Digital Lean Manufacturing Quantifying the Financial Impact of Industry 40 Integration in 2024 - Current adoption rates of Lean 0 among manufacturers

The adoption of Lean 0 among manufacturers is still in its early stages, with many companies struggling to move beyond testing and into full-scale implementation. While some have embraced Industry 4.0 technologies like data analytics and automation to improve efficiency, many others remain stuck in pilot phases, unable to overcome the hurdles of merging these digital tools with traditional lean practices. There are numerous challenges, including concerns about cybersecurity, worker resistance to automation, and a lack of clear leadership to guide the transition. It seems like the promise of massive financial gains from Lean 0 remains largely untapped due to these obstacles.
The adoption of digital lean manufacturing technologies, or "Industry 0" as some call it, is uneven across industries. While automotive manufacturers have embraced it, with around 65% adopting these technologies, the textile industry lags behind at around 30%. This difference reveals significant disparities in preparedness and capability across sectors.
Leading manufacturers report a remarkable 35% improvement in Overall Equipment Effectiveness (OEE) thanks to digital lean techniques. This demonstrates that digital tooling can amplify traditional lean principles, going beyond just waste reduction.
However, despite the hype, predictive maintenance, a cornerstone of digital lean manufacturing, doesn't seem to be living up to its full potential. About 50% of manufacturers using predictive analytics for maintenance report less than a 10% reduction in downtime. This raises questions about the effectiveness of current predictive models in complex manufacturing environments.
Many manufacturers, close to 40%, are facing bottlenecks in data management due to outdated legacy systems. This hinders their ability to fully embrace Industry 0 integration and unlock its promised efficiency gains.
While lean principles are often associated with streamlining processes and reducing bureaucracy, companies integrating digital tools are finding themselves needing more structured frameworks and governance. Around 60% of companies believe that increased oversight is necessary for effective implementation.
A major concern is cybersecurity, acknowledged by over 70% of executives as a critical barrier to adopting Industry 0 practices. This significant risk factor remains largely unaddressed by many organizations.
A surprising finding is that nearly 45% of manufacturers report employee resistance to digital tools. This highlights the challenge of cultural adaptation, which can undermine both lean and digital initiatives if not properly managed.
Despite the hype, the payback period for digital lean manufacturing investments is turning out to be longer than initially anticipated. While the average sits around 2.5 years, this is significantly longer than the projected two-year mark. This discrepancy can be attributed to unforeseen integration hurdles and the mismatch of expectations in complex manufacturing environments.
However, companies that adopt an agile approach to integrating Industry 0 technologies are reaping significant rewards. They're reporting profit margin increases of up to 15%, contrasting sharply with the overall industry performance that often remains stagnant.
It's clear that the adoption of Industry 0 is a complex process. While the potential benefits are undeniable, companies need to overcome the challenges and manage the transition effectively to fully reap its rewards.
More Posts from financialauditexpert.com: