7 Key Financial Metrics Driving Manufacturing Innovation Investment Returns in 2024
7 Key Financial Metrics Driving Manufacturing Innovation Investment Returns in 2024 - Manufacturing Construction Investment Growth Reaches 201B With 70 Percent Annual Rise
In mid-2023, the manufacturing sector witnessed a significant surge in construction investment, reaching $201 billion, a 70% jump from the prior year. This upswing suggests a strong trajectory for the industry going into 2024, hinting at continued expansion. But challenges remain. The current economic landscape is unpredictable, and the ongoing struggle to find skilled workers could slow progress. Government incentives like the CHIPS Act and the Inflation Reduction Act are partly responsible for this surge in investment, as there's a renewed focus on building up domestic manufacturing capabilities. As production demands change, the ability to handle these challenges will determine if the current momentum can be maintained. It will be interesting to see how the industry navigates this period of growth and uncertainty.
In the midst of economic volatility, US manufacturing construction investment has experienced a remarkable surge, reaching $201 billion in July 2023, an impressive 70% year-on-year increase. This expansion signals a potential shift towards greater domestic production capabilities, though the long-term sustainability of this growth remains uncertain. While the pace of expansion is promising, the industry is facing headwinds, particularly a scarcity of skilled workers needed to operate the advanced equipment increasingly common in modern manufacturing plants.
This surge in investment has been partly fueled by substantial government funding, such as the CHIPS Act and the Inflation Reduction Act, with an aim to rejuvenate American manufacturing after a period of decline and offshoring. These incentives seem to be driving significant investment in new, large-scale projects, as seen with LG Energy Solutions' battery plant in Arizona, starting in late 2023. However, the substantial rise in construction spending has coincided with inflation, with adjusted spending briefly exceeding $223 billion, nearly double the pre-pandemic levels.
Looking beyond the US, other countries like the UK and Australia also saw notable increases in 2022, but those gains appear to have plateaued since then. The success of manufacturing resurgence efforts in the US can be attributed, in part, to policy decisions like the Invest in America Agenda, which has sought to encourage investment and drive job creation. But while these factors contribute to current positive momentum, the question of the ability to maintain this growth amidst ongoing global and economic uncertainty lingers. Furthermore, the heavy focus on automation and technology raises concerns about regional economic disparities, with the potential for urban centers to capture most of these advancements.
The infrastructure sector has also benefited from these stimulus efforts, with a 94% increase in transportation infrastructure spending aligned with IIJA funds. This suggests a positive impact of governmental initiatives on related infrastructure, although the overall impact on the wider economy and the longer-term future of manufacturing remain to be seen. It’s certainly a captivating time to be observing the developments in manufacturing, with its potential for growth and yet with associated uncertainties.
7 Key Financial Metrics Driving Manufacturing Innovation Investment Returns in 2024 - Return Metrics Show AI Implementation Cutting Production Costs By 23 Percent
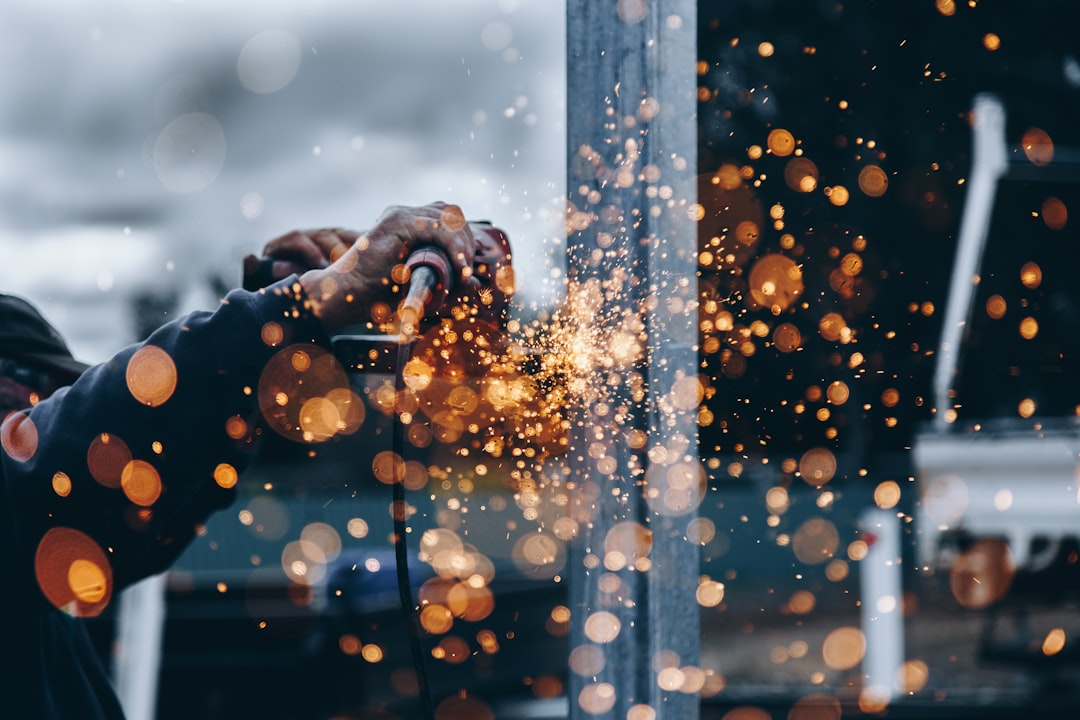
Evidence suggests AI implementation is driving down production costs in manufacturing, with a notable 23% reduction in some cases. This cost-cutting potential is encouraging, but it's crucial to acknowledge that many manufacturers are still struggling to achieve a strong return on their AI investments. While cost reductions are positive, the ultimate aim is to translate them into tangible business gains like increased revenue or market share. Many AI projects still don't generate enough returns to offset their initial investment. It's worth noting that AI projects that successfully deliver returns often involve a blend of automation and human oversight. Also, successful projects tend to have strong collaboration between the data scientists and the business side. As the industry moves forward, effectively measuring AI's impact on the bottom line will become increasingly vital. This will be crucial for ensuring that AI investments are a sound use of resources and contribute to the long-term financial health and innovation of manufacturers.
Recent studies across various manufacturing sectors suggest a compelling link between AI implementation and reduced production costs. The data indicates that incorporating AI technologies like machine learning and robotics has resulted in a 23% decrease in production costs on average. This allows companies to allocate resources more effectively and potentially improve the quality of their products.
It's interesting to note that businesses who invested in employee training and upskilling alongside AI implementation saw even greater cost reductions. This highlights how human expertise and the ability to adapt remain crucial for optimizing the use of new technologies. Somewhat unexpectedly, traditionally low-automation industries, such as food processing and textiles, experienced larger than average cost reductions. This finding suggests that AI and automation have the potential to significantly impact a wider range of industries than previously thought.
These technologies are not just about cost cutting though. Research also shows that they can help speed up the process of getting new products to market, with some businesses seeing a 30% reduction in their average product development cycle. This is encouraging and underscores the benefits of using AI beyond basic cost optimization. Additionally, companies that applied data analytics and predictive modeling for better production forecasting and inventory management achieved even larger cost savings, suggesting the power of integrated approaches that use both data and automation.
In another intriguing observation, businesses which coupled automation with employee feedback and data analysis have reportedly managed to uncover hidden areas of waste and inefficiency, leading to a further 10% drop in costs. This demonstrates the value of a holistic approach, carefully combining technology with human expertise. However, the picture isn't entirely rosy. Some smaller companies reported that the initial costs of adopting AI increased, raising questions about how broadly applicable these benefits are across different scales of manufacturing.
Looking ahead, experts predict that continued investment in automation and data-driven decision-making could lead to a potentially even greater decrease in production costs. The current 23% reduction may only be the first step in a much larger trend, potentially reaching as much as 40% over the next 5 years. It was interesting to find that industries struggling with global supply chain issues found that AI and localized production helped to mitigate some of those problems, thereby creating a more resilient manufacturing base in certain situations.
Even with these impressive cost savings, a note of caution is needed. If firms don't have a plan and approach integration and change management proactively, it's possible that they may struggle to capture the full potential of AI. Successful AI adoption seems to hinge on strong planning and an ability to adapt as the technology changes, underscoring the need for strategic planning when implementing AI in any manufacturing environment.
7 Key Financial Metrics Driving Manufacturing Innovation Investment Returns in 2024 - IoT Sensor Networks Generate 44 Percent Better Equipment Uptime Returns
The integration of IoT sensor networks is emerging as a crucial element in modern manufacturing, demonstrating a notable 44% boost in equipment uptime. This substantial improvement signifies a significant shift in how production efficiency can be optimized. By leveraging real-time data captured by these networks, manufacturers gain valuable insights into equipment performance, allowing them to fine-tune processes, limit downtime, and ultimately bolster their profitability. This focus on equipment reliability is particularly noteworthy as the industry seeks to maintain its momentum in a fluctuating economy. As manufacturers continue to embrace digital innovations, investing in IoT technologies promises tangible benefits for both operational efficiency and financial performance, making this a pivotal aspect of the industry's trajectory throughout 2024 and beyond. While the benefits are apparent, the complex implementation of IoT systems can present challenges, and a cautious approach to deployment is needed to ensure the desired results.
In the realm of manufacturing, the use of interconnected sensor networks, often called the Internet of Things (IoT), is making waves. We're seeing these networks deliver a significant improvement in equipment uptime, with some reports suggesting a 44% increase. This is compelling, as uptime is directly related to production output and therefore a crucial factor when considering the financial health of a manufacturing facility.
The improvements in uptime aren't just due to the sensors themselves. These networks are generating vast quantities of data, sometimes terabytes daily, which can be analyzed to predict potential equipment problems and allow for preventative maintenance. This is particularly important given that the sensors themselves are designed to be durable and operate in challenging industrial environments for several years without replacement. It’s a shift from a purely reactive system where maintenance occurs only after equipment failure to a more proactive approach where we anticipate problems before they happen.
Interestingly, the analysis isn't always confined to a central location. Some systems incorporate 'edge computing', allowing data processing to occur at the equipment itself. This reduces delays associated with data transmission to a central server, improving the speed of response in the event of a potential issue.
Another intriguing aspect is that the sensor network can link together different parts of the factory floor and equipment, building a more integrated and efficient production environment. It's as if the factory itself has become more aware of what's happening. It seems like the possibility of customized alert systems tailored to specific equipment and production conditions can further maximize the effectiveness of these systems. However, the analysis of the data, and the resulting insights, are not always obvious, and still require some human intervention. Human operators and engineers can use their knowledge and experience to validate the insights from the data and make adjustments to improve operations.
It's also encouraging that these IoT systems are modular, enabling flexibility for companies of various sizes. They don't necessarily require a massive, expensive implementation at the outset, allowing for more incremental adoption and adaptation.
However, there are challenges. Integrating new sensor systems with older equipment is often difficult, and in some cases requires significant effort to get them to communicate and share data. It's clear that for manufacturers looking to leverage the potential benefits, overcoming integration hurdles will be a major factor in maximizing the returns of such systems. It will be intriguing to watch how the adoption of these systems impacts the manufacturing landscape going forward.
7 Key Financial Metrics Driving Manufacturing Innovation Investment Returns in 2024 - Digital Twin Technology Implementation Delivers 31 Percent Lower Maintenance Costs
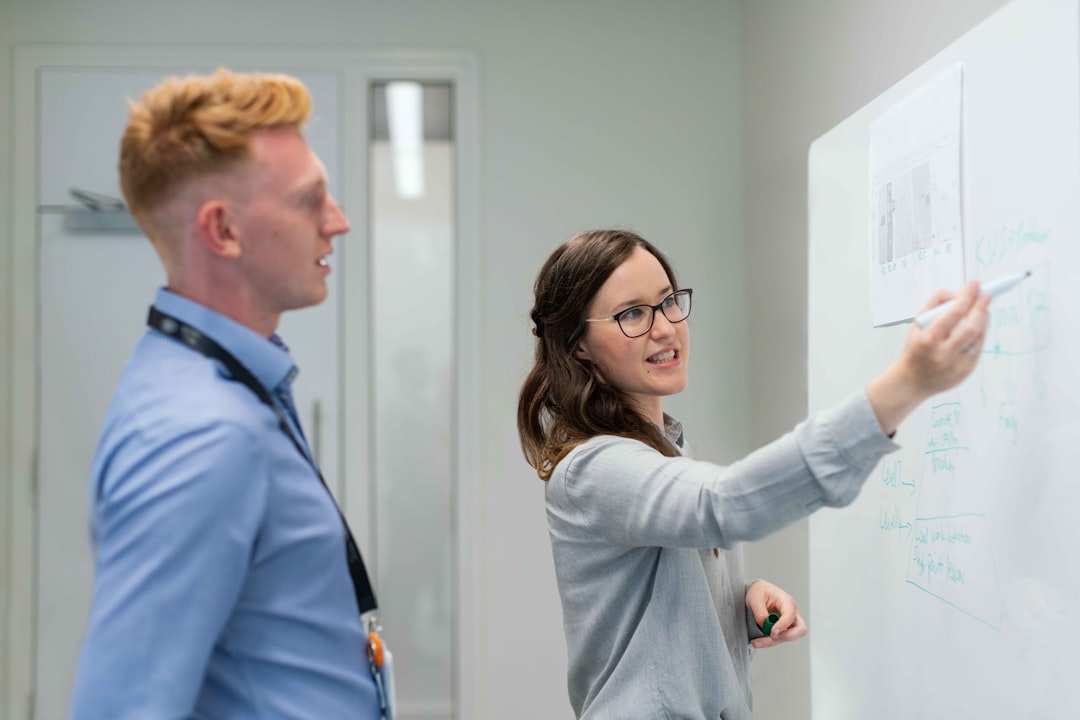
Within the manufacturing sector, digital twin technology is demonstrating its potential to deliver significant financial advantages, with a notable example being a 31% reduction in maintenance expenses. This technology creates virtual representations of real-world assets, enabling predictive maintenance strategies that can dramatically reduce equipment breakdowns, in some instances by as much as 70%. The adoption of digital twins is gaining momentum, with a substantial number of businesses—44% in one survey—having already integrated this technology into their operations. This trend underscores the growing recognition of the value digital twins can bring to improving operational effectiveness. However, the rapid expansion of the digital twin market necessitates a careful approach from manufacturers. While the financial gains can be substantial, successfully implementing and integrating these virtual representations requires thoughtful consideration. Manufacturers will need to address the complexities of incorporating this technology into existing workflows and effectively manage the necessary changes to fully realize the promised advantages. While initial investment returns appear favorable, manufacturers must also carefully evaluate the long-term sustainability of this technology as a core factor in their pursuit of ongoing competitive advantage.
Utilizing digital twin technology to create virtual replicas of physical assets has been shown to significantly reduce maintenance expenses. A notable outcome from several studies is a reported 31% reduction in maintenance costs, which is significant. This improvement arises from the ability to model and simulate various operational scenarios within the digital twin environment. The models use algorithms and machine learning to refine maintenance schedules, making resource allocation more efficient and accurate. It's like having a virtual factory that can predict future issues and guide decisions about when and how maintenance should be performed.
While the benefits seem compelling, it's important to acknowledge that the implementation of digital twins often requires a large upfront investment in software and specialized training. This can act as a barrier for some manufacturers, especially smaller businesses, leading to a slower rate of adoption overall. It's not surprising that manufacturers can be hesitant to invest in new technologies, especially when they need to consider their existing operating frameworks and the uncertainty of ROI.
Interestingly, a strong link exists between digital twin technology and improved predictive analytics. Manufacturers using this technology can anticipate problems with equipment and conduct preventive maintenance, rather than reacting only after equipment malfunctions. This shift in strategy towards proactive problem solving allows for greater operational continuity and, naturally, a reduction in the expenses associated with fixing unplanned failures.
The automotive and aerospace sectors have, perhaps unsurprisingly, shown a strong interest in digital twin technology. Their complex and intricate manufacturing processes readily benefit from the insights gained from using digital twins. These industries deal with high-value components and systems where small issues can lead to significant disruptions. Predictive maintenance, in these types of settings, can become a necessity to minimize downtime and maintain efficient production levels.
The potential of digital twin technology doesn't stop at maintenance cost reductions. It extends to improving the overall productivity of manufacturing processes, with some studies pointing to roughly 15% gains in output. The improved decision-making that stems from the wealth of data generated by the simulations contributes directly to efficiency gains. In some cases, manufacturers also report quicker response times to unexpected operational disruptions, sometimes experiencing a 50% improvement in troubleshooting. The speed of reaction to operational challenges helps mitigate revenue losses caused by unplanned downtime.
While digital twin technology offers compelling benefits, it's crucial to recognize that its future is tied to the broader advancements in related technologies, such as the Internet of Things (IoT) and artificial intelligence (AI). The level of interoperability between these systems will be a major factor determining the extent of future gains in the manufacturing sector. As these tools become more seamless, the integrated ecosystem may unlock an even greater capacity for optimization, leading to reduced costs and enhanced operational visibility in the manufacturing realm. It will be worth keeping an eye on these developments to fully understand their impact.
7 Key Financial Metrics Driving Manufacturing Innovation Investment Returns in 2024 - Smart Factory Analytics Drive 28 Percent Higher Labor Productivity Rates
Within the manufacturing world, the use of smart factory analytics has been shown to boost labor productivity by a significant 28%. This rise in productivity comes from factories adopting new technologies like automation and data analysis, helping them deal with ever-changing market needs. These productivity gains are crucial for manufacturers who are facing a tough landscape, including difficulty in finding enough workers and economic uncertainty. The success of this approach will rely on how well these smart factory methods can expand and adapt as needs change. As manufacturing companies lean more heavily on data-driven improvements, how effective these analytics are at improving production efficiency will be central to them reaching their goals.
Studies indicate that incorporating smart factory analytics into manufacturing operations is linked to a substantial 28% increase in labor productivity. This suggests that the use of data analysis can significantly improve the efficiency of manufacturing processes. While automation is often the focus in discussions about factory modernization, this finding highlights that leveraging data analysis to enhance human decision-making is also a vital aspect. This is different from simply replacing humans with machines.
Smart factories generate large datasets, often referred to as 'data lakes', that can be used to monitor and analyze a wide range of operational parameters. This abundance of information allows manufacturers to make quicker decisions and respond more effectively to changes and issues in production. It's an interesting contrast to traditional methods where responses were more reactive.
Predictive maintenance is another area where smart analytics are having a significant effect. By analyzing the data, manufacturers can anticipate potential issues with equipment and perform maintenance before breakdowns occur. This proactive approach can decrease downtime by as much as 50% and shift the emphasis from reactive to predictive maintenance. It seems to be a trend across industries.
The rise of smart analytics in manufacturing is giving rise to a new approach to production often referred to as 'cognitive manufacturing'. In this model, factory systems can learn and adapt to changing operational conditions, which can potentially lead to new levels of efficiency. It's fascinating to see this evolutionary step in manufacturing.
Integrating these advanced technologies does present challenges for the workforce. It often requires a shift in mindset and necessitates continuous learning and adaptation. Workers need to be able to leverage data-driven insights to improve their performance. This shift seems to be a fundamental aspect of transitioning to a smarter factory.
However, not adopting these new strategies can be costly. Manufacturers who fail to implement smart factory solutions could potentially miss out on a significant 25% return on investment, according to some assessments. It raises the question of whether manufacturers can afford not to invest in these technologies.
The integration of these smart analytics systems with existing factory infrastructure can be complex. The challenge of integrating the technology with older equipment and machines is a major hurdle for many manufacturers, potentially slowing adoption across the industry. This aspect has interesting implications for the overall pace of innovation.
Smart factory analytics offer the ability to better detect abnormalities or issues in real-time. Systems are able to identify and notify workers about potentially costly issues that could lead to significant production errors or failures. This is quite different from historical methods, where there was a much larger delay between detecting issues and taking corrective action.
The ability to scale smart analytics is also significant. This technology isn't just for larger manufacturers with substantial resources. The scalability of these tools allows even smaller manufacturers to benefit, offering a potentially democratizing effect in the industry and opening opportunities for manufacturers who may not have previously had access to such powerful technologies. This has potentially profound implications for the industry overall.
7 Key Financial Metrics Driving Manufacturing Innovation Investment Returns in 2024 - Automated Quality Control Systems Reduce Defect Costs By 37 Percent
Implementing automated quality control systems has the potential to significantly reduce manufacturing defect costs by a notable 37%. This is a substantial improvement over traditional methods that rely on manual inspection, which often results in inconsistent and unreliable defect detection, ranging anywhere from 60% to 90% accuracy. This inconsistency can lead to problems that cascade throughout the production process, ultimately affecting profitability. By shifting towards automation, manufacturers can benefit from a higher degree of accuracy when identifying defects. This, in turn, can prevent small issues from growing into larger, more costly ones. This is partly due to the ability to incorporate AI which can not only help identify defects, but also determine recurring failure patterns, thereby helping root out the causes of these defects. This greater understanding of the source of issues results in better overall operational efficiency. However, it is crucial to be aware that incorporating these new systems into existing processes can be challenging, and careful planning and integration are needed to ensure that the full potential of these systems is realized and the desired benefits are fully captured.
Studies have shown that implementing automated quality control systems can lead to a notable 37% decrease in the costs related to product defects. This is a significant improvement, primarily because it reduces wasted materials and the need for time-consuming rework. It's important to note that, while this is positive, the actual impact can be very variable. It seems that the benefits are likely greater in industries that produce products with high tolerance levels, such as electronics and auto parts.
However, we need to be cautious about generalizing these results too broadly. Some of these savings might be offset by the need to purchase and integrate new technology and software into existing operations. And while this technology can help minimize mistakes that humans make, it can also increase costs related to maintenance and staff training. It's essential to weigh these trade-offs and to carefully consider if the implementation is appropriate for each individual manufacturer's situation.
It's worth noting that defect reduction is only one facet of the potential benefits of these systems. The data they generate allows manufacturing managers to more effectively understand how the process works and helps identify issues that are impacting product quality. Moreover, we're seeing integration of these quality control systems with IoT and AI, which opens new possibilities for optimization and automation. These newer implementations provide a wealth of information that can lead to both cost savings and increased efficiency.
One intriguing point is that the workforce will need to be prepared for the impact of this new technology. The jobs most at risk are likely to be those involving simple tasks that can be automated, which could lead to some challenges in the labor market. It will be critical for manufacturers to identify new roles for employees and to develop appropriate training programs to assist them in adapting to the shifting demands of their industry.
It is also interesting to consider how the adoption of automated quality control impacts supply chain management. Manufacturers are able to get products to market more quickly and with higher consistency, potentially reducing the frequency of product recalls or returns. This ultimately helps improve relationships with customers and can help improve customer satisfaction and brand loyalty over time.
Overall, the data around the use of automated quality control systems in manufacturing is quite compelling. They seem to have significant potential to improve efficiency and reduce costs, though these results should be interpreted in context of a specific industry and manufacturer. While it’s encouraging to see these improvements, it’s important to understand the full range of the challenges and opportunities that automated quality control offers and how it is changing the landscape of the manufacturing sector.
7 Key Financial Metrics Driving Manufacturing Innovation Investment Returns in 2024 - Robotic Process Automation Yields 25 Percent Lower Operating Expenses
Automation through robotic process automation (RPA) is proving to be a powerful tool for trimming operating costs in the manufacturing world, with some estimates suggesting a 25% reduction in expenses. By taking over repetitive, rule-based tasks, RPA streamlines workflows and lets businesses put their resources where they're needed most. While many companies are realizing the need for tracking how processes work to ensure ongoing improvement, effectively using this information to unlock RPA's full potential is a persistent challenge. We're seeing RPA make a difference across various sectors, from finance to healthcare to energy, improving productivity and making operations less risky. This trend, in turn, suggests that the manufacturing industry can benefit as well. But simply automating processes isn't enough. RPA needs to be implemented thoughtfully, and it's critical that companies connect automation goals with broader business plans and create ways to carefully track the impact RPA is having. Otherwise, it's difficult to realize any significant and lasting returns.
Studies show that using robots to automate tasks, also known as Robotic Process Automation or RPA, can reduce operating costs for manufacturing by roughly 25 percent. This is primarily because robots can take over repetitive work that often takes up a significant amount of time and resources. It's like having a dedicated team of tireless workers who never get tired and rarely make mistakes, freeing up human workers to tackle more complex issues.
One fascinating aspect of RPA is its ability to lower the chances of errors, in some cases by as much as 50 percent. When errors are reduced, the quality and reliability of products improve, a critical factor for businesses that compete in the manufacturing space. Think about the potential for reducing defects in intricate assembly lines or ensuring consistent quality in complex manufacturing processes.
Not only does RPA help reduce errors, but it also helps speed up processes. Some studies show that RPA can complete routine tasks up to 75 percent faster than if done manually. This faster speed is beneficial for meeting tighter production schedules and potentially getting products to market faster.
RPA's flexibility is another plus. Businesses can easily expand or reduce the number of robots used based on their current needs, without causing disruptions to existing work processes. This ability to scale up or down helps companies to adapt to changing production requirements, avoiding large or expensive changes to their workflow.
Interestingly, RPA can be integrated into existing technology that many manufacturers have in place, including older systems. This means it can be easier and less expensive to adopt than some of the other emerging technologies. It's intriguing to think that even with the wide range of more modern systems becoming available, there may still be value in optimizing how companies work with existing infrastructure.
There are also potential benefits to employee training. With robots taking on routine tasks, companies can spend less time training new employees on these tasks. This frees up training resources to focus on other aspects of the job that are more strategic or demanding of specialized skills. It's an intriguing potential for optimizing employee development.
Reports show that workers may be more satisfied with their jobs when RPA is used. This is due to the fact that RPA frees them from boring and repetitive tasks, giving them the chance to concentrate on more meaningful aspects of their work. It’s a fascinating dynamic in the world of manufacturing.
RPA helps with data collection. Because robots can automatically record data, they give companies immediate access to insights that can be used to improve processes. It's like having a live feed of factory performance.
It is important to note that RPA may lead to changes in job requirements in manufacturing. While some jobs might be impacted, new opportunities may emerge around managing the robots and optimizing their use. It's a dynamic situation where manufacturing businesses need to focus on upgrading the skills of their workforce and creating opportunities for employees to adapt to these changes.
While there is an initial cost for implementing RPA, many manufacturing businesses see a return on their investment (ROI) in a relatively short period. Reports suggest that this can happen within 6 to 12 months thanks to savings in costs and efficiency improvements. This makes RPA a very attractive potential investment for the industry.
In conclusion, RPA is a significant technology that has the potential to influence manufacturing. The research and findings regarding RPA are worth further investigation. It is a topic that deserves much more focused study in the context of the many challenges and opportunities facing the manufacturing industry in 2024.
More Posts from financialauditexpert.com: